罗茨水环机组:塑胶厂“全年无休”的硬核生产力引擎
在塑胶加工行业,设备宕机是悬在生产线上方的“达摩克利斯之剑”。传统真空泵因故障频发、能耗失控,常让企业陷入“停机抢修—订单积压—利润缩水”的恶性循环。而罗茨水环真空机组的出现,正以“全年无休”的稳定性、“三防一体”的硬核性能,重塑塑胶厂的生产逻辑。工人从“救火队员”变身“巡检员”,老板直呼“省下的钱够换辆特斯拉”——这场由真空系统引发的效率革命,正在颠覆行业认知。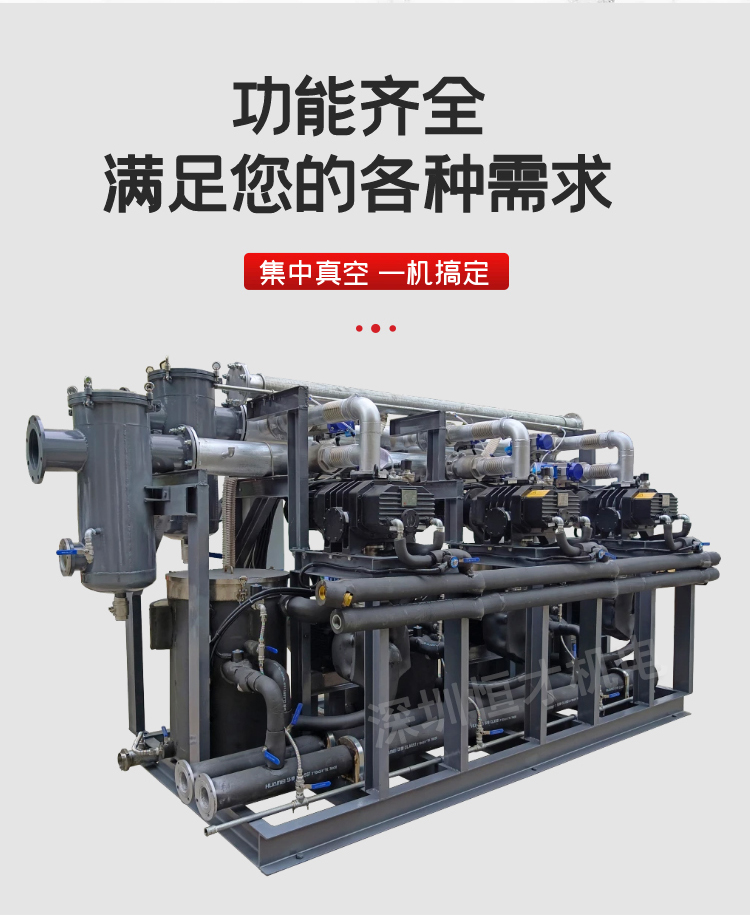
一、传统泵之殇:塑胶厂的“午夜惊魂”
在一家年产值2亿元的家电外壳塑胶厂,传统旋片泵的“暴雷”时刻堪称生产部的噩梦:
故障频发:粉尘与脱模剂混合形成的油泥,每月导致旋片泵卡死3~5次,单次抢修耗时4小时,单日产能损失超15万元;
真空度跳水:加工冰箱内胆吸塑件时,因真空度波动±25%,产品壁厚不均率高达18%,客户退货率攀升至行业均值3倍;
能耗黑洞:为维持真空度,旋片泵需持续高负荷运转,单台设备年耗电28万度,电费成本占加工总成本的17%。
更致命的是,传统泵的“随机故障”常在深夜爆发。某次大单交付前夜,因真空泵突然停机,12条生产线被迫停摆,管理层连夜从50公里外调设备救急,直接损失超80万元。这类“午夜惊魂”事件,已成为中小塑胶厂的“行业诅咒”。
二、罗茨水环机组:破解“不可能三角”的工业奇迹
罗茨泵与水环泵的“黄金组合”,通过技术创新实现了“高真空、抗粉尘、低能耗”的完美平衡,其核心突破体现在:
粉尘克星:自清洁密封系统
罗茨泵采用“迷宫密封+气体吹扫”双保险设计,转子间隙0.3mm处形成动态气帘,可实时吹散直径0.1mm以上的粉尘颗粒。水环泵以水为密封介质,彻底规避油雾污染。某玩具吸塑厂实测数据显示,改用该机组后,粉尘堆积引发的故障率从42次/年降至1次/年,设备MTBF(平均无故障时间)从280小时跃升至8760小时。
真空跃迁:三级压缩技术
罗茨泵负责粗真空阶段(大气压至1000Pa)的高速抽气,水环泵在1000Pa以下接力压缩,形成“接力式”真空梯度。在汽车仪表盘加工案例中,该机组实现:
真空建立速度:0.8秒达成-98kPa,较传统泵提升300%;
极限真空度:稳定在-99.5kPa,使片材拉伸率从180%提升至240%,产品棱角锐度提升40%;
真空度波动:控制在±1.5kPa以内,彻底消除鼓包、麻点等缺陷。
能耗革命:智能变频+热能回收
机组搭载AI变频算法,可根据模具真空需求实时调节电机转速。某化妆品包装厂改造后:
单件能耗:从0.28度降至0.11度,年省电费126万元;
热能回收:水环泵循环水中的余热被导入模具预热系统,减少天然气消耗35%;
碳足迹削减:单条生产线年减排CO₂ 187吨,相当于种植10300棵树。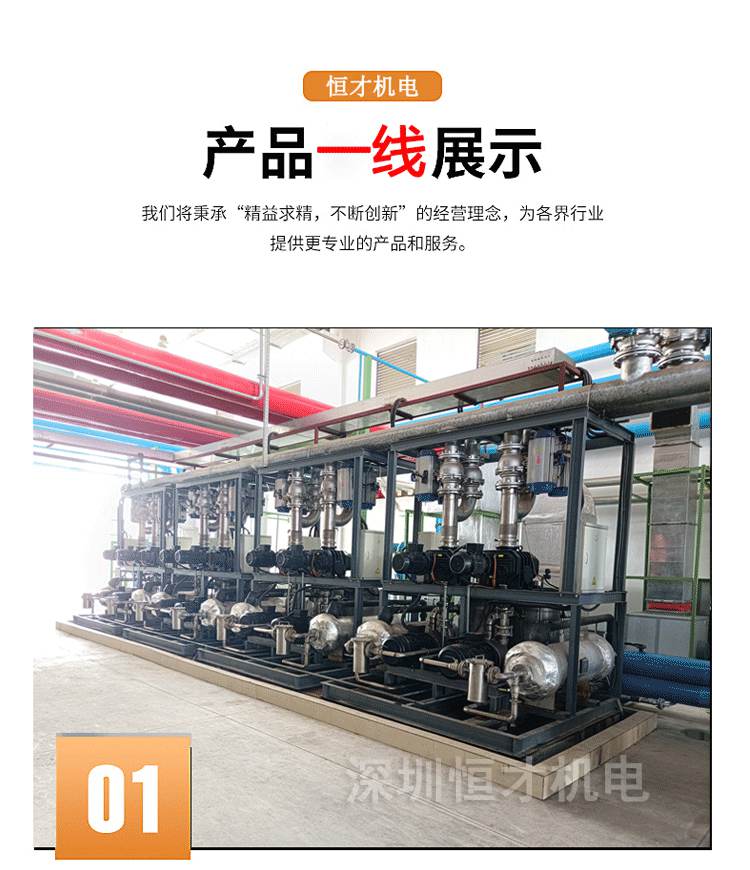
三、实战革命:从“故障抢修”到“躺赢生产”
某家电巨头的生产线重生
该企业原使用12台2BV水环泵+旋片泵组合,因粉尘堵塞导致年停机192小时,良品率仅83%。更换罗茨水环机组后:
设备OEE(综合效率):从62%提升至91%;
单线产能:从日产8000件跃升至14500件;
维护成本:年维修费用从87万元降至12万元,降幅达86%。
医疗器械包装厂的“零缺陷”突破
在医用透析器外壳吸塑中,传统泵因真空度不稳导致产品壁厚公差±0.15mm,远超0.05mm的医疗级标准。改用罗茨水环机组后:
真空精度:达到±0.02kPa,使产品壁厚公差缩小至±0.03mm;
洁净度:通过ISO 14644-1 Class 7认证,粉尘残留量<0.5μg/m³;
认证效率:一次性通过FDA审核,产品溢价能力提升25%。
四、选型与部署:避开“伪节能”陷阱
科学选型四原则
抽速匹配:按公式Q=K×S×H(Q为抽速,S为模具面积,H为片材厚度,K为1.3~1.5安全系数)选型;
级配优化:罗茨泵抽速应为水环泵的4~6倍,例如500m³/h水环泵需搭配2000~3000m³/h罗茨泵;
材质升级:接触真空侧部件采用316L不锈钢,耐腐蚀性提升10倍;
智能扩展:预留物联网接口,支持远程诊断与预测性维护。
部署避坑指南
管路设计:真空管道内径需≥泵口直径的1.2倍,弯头数量≤3个,阻力损失降低40%;
水环泵温度控制:循环水温度保持在15~25℃,每升高1℃抽速下降2%;
粉尘预处理:在机组前加装旋风分离器,过滤效率≥99.5%,延长设备寿命3倍。
五、未来图景:从“设备内卷”到“生态共赢”
随着工业4.0的推进,罗茨水环机组正从“单机神器”进化为“智能生态节点”:
数字孪生系统:某头部企业已实现真空系统与MES、ERP的深度对接,通过AI算法优化排产,使设备利用率提升22%;
能源银行模式:部分厂商推出“真空即服务”(VaaS),企业按实际抽气量付费,初期投入降低70%;
循环经济闭环:水环泵废水经纳米过滤后可循环使用,配合光伏发电系统,单条生产线年碳收益达58万元。